If you work with glass, you deal with scratches. Beyond costing you time, money, and business, scratched glass is just a straight-up pain. Most people either throw out the scratched piece or cause more damage while removing scratch. Sound familiar? It’s time for a better way. With the Gforce Max, distortion-free scratch removal is not only possible—it’s also amazingly simple.
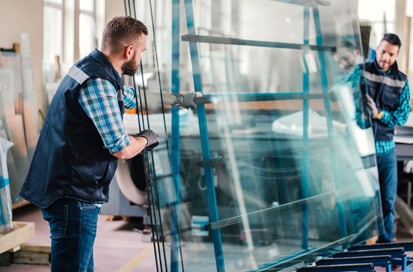

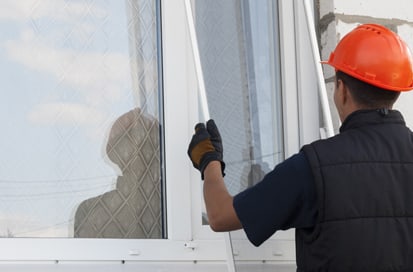

DISTORTION-FREE
Anyone who says distortion-free isn’t possible hasn’t met the Max. Our one-step technique doesn’t remove glass from the surface. Instead, it uses heat, friction, and compound to level out the damage. Think of it like ironing wrinkles out of clothes.

ONE-STEP
With the Max, removing scratches won’t put you behind schedule. Our one-step technique, which can be used for 90% of scratches, only uses one disk. In fact, most damage can be removed in just a couple minutes.

EASY-TO-LEARN
Scratch removal doesn’t have to be complicated. The Max is so straightforward that even beginners are just a training video away from successfully removing scratches. We also have extensive resources to prepare you for every scenario.

CLEAN
Most scratch removal systems create a mess so big that it’s not worth the hassle. In conjunction with the Splash Guard, the Max minimizes splatter and keeps your area tidy. No need to stress about clean-up.
Types of Glass

Tempered
Including doors and showers

Laminated
Including windshields

Mirror
Including bathroom and decorative

Annealed
Including windows
FAQs
What makes the Max different than other scratch repair systems?
The Gforce Max is the only tool designed specifically for removing scratches. It’s main features include:
- Built-in Water Feed: No need for a handheld water bottle. Water is released through a convenient, built-in button.
- Ergonomic Grip: The grip was designed specifically for comfort and fatigue prevention.
- Self-leveling Backer Pad: The self-leveling backer pad makes it easy to keep the disk level on the glass.
Many scratch removal systems claim to be distortion-free, but if they use abrasive disks, that’s impossible. Any time glass is removed from the surface, distortion can happen.
Our One-step Technique is able to achieve distortion-free results through a combination of heat, friction, and Polishing Compound. Glass is not removed during the process.
Can scratches be removed from all types of glass?
Yes, the GForce Max is designed to remove scratches from almost all types of glass including tempered, laminated, mirrors and annealed. Certain techniques may be required based on the severity of the scratch. We do not recommend scratch removal for textured or coated glass.
How long does scratch removal take?
Our One-Step technique is a distortion-free process that allows you to remove most scratches in just minutes. It’s great for repairing light-to-medium scratches caused by handling, transportation, glass-on-glass rubs, razor blades, light sand paper, and windshield wipers.
Is scratch removal truly distortion-free?
Yes! The GForce Max System works differently because it applies a light amount of heat and friction instead of abrasion like other systems. Our polishing compound works to remove the scratch, not the glass, at a molecular level and smooth over the area. This creates a distortion-free result, with way less time and skill involved.
What training is available for beginners?
We’ve made learning the GForce Max easy. After watching our training video and about an hour of practice, even inexperienced users will look like pros. Still have questions or just want to see the GForce Max in action? Schedule a live virtual demo with the team HERE!
What if I have deeper scratches?
Our Multi-Step Technique uses micro-abrasive disks to remove medium-to-heavy scratches caused by graffiti, carbide scrapes, welding, logos, heavy sand paper,and masonry.
Questions? We’re here to help. Call us at +1 (541) 388-1156 or fill out this form.